Laser Marking Systems / Laser Markers
Laser Marking in the Electric Vehicle Industry
-
Tags:
- Laser Marking , Battery , Laser Cleaning
Amid growing exhuast regulations around the world, the development of electric vehicles is accelerating. The components needed for electric vehicles differ drastically from the conventional gas vehicle; however, similar to gas vehicles all these components need some form of identification or traceability marks. The intricacies of electrical components like batteries, connectors, converters, inverters, ECU's, etc. make traceability a concern for most marking methods. Laser making on the other hand delivers the precision, quality, and permanency that alleviates these concerns.
Direct Part Marking in the Electric Vehicle Industry
This section introduces marking and printing applications useful in the electric vehicle (EV) industry. In recent years, laser marking has become widely used to mark electric vehicle parts and components, such as the vehicle's make and model, as well as its serial number. This helps to ensure that these parts and vehicles can be traced back to their manufacturer when they need to be repaired or serviced.
Laser marking electric vehicles is a quick, efficient, and reliable way to provide this information, and it can be used on a wide variety of surfaces, including metal, plastic, and glass. It is often used on both EV batteries and ECUs. Additionally, laser marking can be used to add aesthetics to EV parts. This can include company logos, slogans, or other designs.
Discover more about this product.
Click here to book your demo.
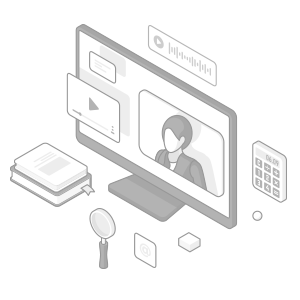
Laser Marking on Batteries (Electrodes and Insulation)
Batteries are the primary power source of electric and hybrid vehicles. They regain their power through direct charging or vehicle deceleration. Automotive manufacturers recently started using lithium-ion batteries, which have a larger capacity and a more compact/lightweight design compared to traditional options.
A: 2D Code and Serial Number Marking on the Battery Cover
A battery has a case and a cover, which are marked for traceability to optimise manufacturing and assembly.
B: Battery Cover Surface Roughening
Laser light is used to roughen the adhesion surface of the battery cover and case to improve the bonding strength.
C: 2D Code Marking on Electrodes
2D code marking is becoming widespread. In the past, only battery cases were marked. Now, there's an increasing need to mark individual electrodes along with the case.
Laser Marking on Inverters
Inverters convert stored electricity from DC to AC and supply AC to the motor. Because motors rotate over a wide angle while a vehicle is operated, inverters must meticulously control the supplied electricity.
A: 2D Code and Character String Marking on PCB
Glass epoxy PCB marking must be damage-free to prevent particle generation on photo-resist removal.
B: 2D Code Marking on Cooling Device
Marking a 2D code on the cooling device makes it very easy to ascertain the device specifications.
C: Serial Number Marking on the Case Cover
Affixing labels to an inverter's case is common, but labels are expensive to produce and can't accommodate design changes well. Laser markers don't incur running costs and are very easy to adjust.
D: 2D Code and Character String Marking on Aluminium Cast Parts
Cast aluminium cases can vary in size depending on product tolerances. It's important to have a marking system that can compensate for these size changes, otherwise you run the risk of defective, out-of-focus marks that aren't readable.
We’re here to provide you with more details.
Reach out today!
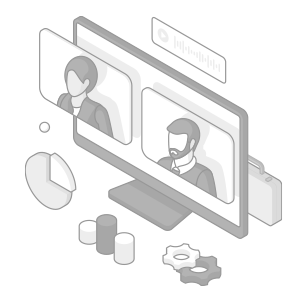
Laser Marking on Sonar Sensors
These sensors are installed in the bumper and detect obstacles up to about 1 m away. They are used in parking and notify the driver of nearby obstacles.
A: Identification Marking on Case
Identification marking is applied to the numerous sonar sensors in the vehicle.
B: 2D Code Marking on Sensor Parts
Sonar sensors come in a wide variety of colours so they can match different coloured vehicles. As a result, traceability systems must be able to cleanly mark a wide range of colours in sonar marking applications.
Laser Marking on Front Cameras
Forward vehicle cameras are used to alert the driver of other vehicles, pedestrians and traffic signs. Cameras are good at detecting relatively close objects and can recognise white lines indicating traffic lanes, crosswalks and speed limit signs.
A: Identification Marking on Lens Unit
Identification marks are placed on the ring that fits around the camera lens.
B: Character String and 2D Code Marking on E-coated Parts
Lasers are used to mark e-coated parts on the camera's base. To ensure rust prevention, the marks must not completely remove the paint.
We’re here to provide you with more details.
Reach out today!
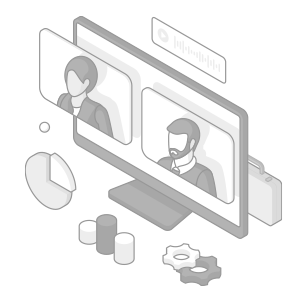
Laser Marking on Rear Cameras
Rear-facing vehicle cameras display the area behind a vehicle. This video feed is displayed on the navigation monitor when the vehicle is backing up. Rear cameras often use CMD lenses because they are able to display the left, right and centre areas behind a vehicle.
A: Serial Number Marking on Camera Case
Identification marking is performed to distinguish the installed vehicle model and specifications.
B: Lot Number Marking on Lens
Identification marking is performed on the lens to distinguish the assembled case.
Laser Marking on DC-DC Converters
A DC-DC converter drives electrical components in vehicles such as the headlights, wipers, and audio system by converting stored high voltage to a low voltage direct current. Electrical components in vehicles require more and more power, resulting in a need for increased power capacity and a compact, lightweight design.
A: 2D Code and Character String Marking on PCB
Glass epoxy PCB marking must be damage-free to prevent particle generation on photo-resist removal.
B: Serial Number Marking on the Case Cover
Conventionally, affixing labels to the case was common, but laser marking is becoming more popular to reduce costs and simplify design changes.
We’re here to provide you with more details.
Reach out today!
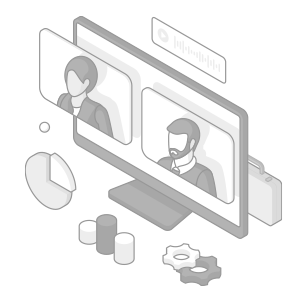
Laser Marking on ECUs
The ECU is the brain of the vehicle, optimising the movement of the various drive mechanisms. It electronically controls the engine, airbags, transmission, and other parts according to operating conditions. ECU development continues to evolve, with higher levels of control obtained every day.
A: Serial Number Marking on the Case Cover
Affixing labels to an ECU's case is common, but labels are expensive to produce and can't accommodate design changes well. Laser markers don't incur running costs and are very easy to adjust.
B: 2D Code Marking for Connector Identification
ECU connectors often use cream-coloured and grey resins, which are difficult to mark with infrared lasers. However, UV lasers are capable of producing high-contrast marks on these materials very easily.
Laser Marking on Milliwave Radars
Milliwave radar sensors detect objects in a large area up to 100 m ahead. Forward sensors measure the distance to the preceding vehicle, rear sensors detect vehicles and pedestrians in blind spots, and front sensors help prevent crossing accidents (that commonly occur at intersections).
A: Standard Marking on Case
All equipment that emits radio waves (such as a milliwave radar) must obtain standard certifications in each country it will be used. Standard certification marks are added each time a new targeted export country is added. Laser markers are optimised for these applications because they easily adapt to design changes.
We’re here to provide you with more details.
Reach out today!
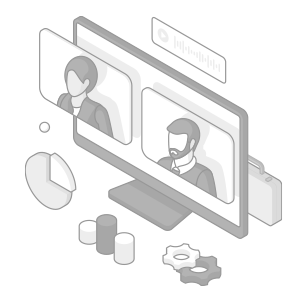
The Importance of Direct Marking in the Electric Vehicle Industry
The electric vehicle industry has seen massive growth in recent years. In 2020, EV sales reached 2.1 million units, up from 1.6 million in 2019. This trend is expected to continue, with Bloomberg estimating just over half of passenger cars sold in the US will be electric vehicles by 2030. The industry has also seen rapid expansion in terms of manufacturing capacity.
This rapid growth is being driven by increasing consumer demand, as well as government incentives and regulations. With EVs becoming increasingly affordable and convenient, the need for laser marking in the industry will continually rise.
Because laser marking is permanent and can be done on a variety of materials, it is an ideal choice for EV manufacturers. Direct laser marking (DLM) is a type of laser marking that is done without the need for any intervening material. This makes direct laser marking perfect for marking objects made of heat-sensitive or delicate materials, which are common inside EVs.
The benefits of laser marking in the automotive industry are numerous. Laser marked components are easier to trace and identify, and they are less likely to be damaged or tampered with. In addition, laser marking can be used to add aesthetic appeal to electric vehicles. When considering all of these factors, it is clear that laser marking is an important part of the electric vehicle industry.
As the industry continues to grow, laser marking electric vehicles will play an increasingly important role in ensuring the safety and traceability of their parts. KEYENCE is a worldwide leader in laser marking systems. Contact us today at 1-800-103-0090 to discuss our EV-specific laser marking solutions.
Contact us to learn more about how our advanced technology can help take your business to the next level.
Contact Us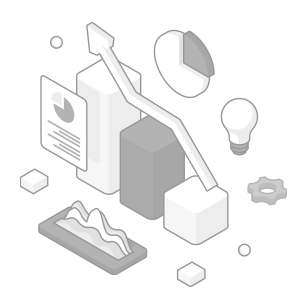
FAQs about Laser Marking in the Electric Vehicle Industry
What are the advantages of laser cleaning over traditional cleaning methods?
Laser cleaning is the most effective method of cleaning for EV battery cells because it is non-contact, higher precision, more repeatable, and minimises the risk of damage relative to other methods.
What types of EV battery cells are suitable for laser cleaning?
All battery cells are suitable for laser cleaning- including prismatic, blade, pouch, and cylindrical cells.
What type of contaminants can laser battery cleaning effectively remove?
Laser battery cleaning is used to remove any contaminants, which includes but is not limited to dust, oil, dirt, grease, adhesives, or battery electrolyte. Lasers vaporise these contaminants, leaving the battery surface free of impurities.
What are the key factors to consider when selecting a laser system for battery cleaning?
The ideal system for laser battery cleaning should feature a high peak power to minimise any threat of thermal damage, while still operating quickly. It should also have maximal beam control for positional precision and consistent power/energy deposition.